Blow-Fill-Seal
A cost-efficient and scalable advanced aseptic process trusted around the world
Blow-Fill-Seal (BFS) is an advanced aseptic process used to fill-finish billions of sterile liquid pharmaceutical doses every year in dozens of markets. In a 3-8 second continuous process (varies by machine model), a plastic container is formed from heated resin, filled with the drug product, and then aseptically sealed.
BFS is designed to scale to any output. A high-end BFS machine can fill and finish up to 15,000 units an hour, with high uptime and low overhead. It uses a very simple supply chain of typically only 1-2 facilities, and its only key raw materials being pharmaceutical-grade virgin resin.
Strong environmental benefits
BFS has always been recognized for its efficiency and low manufacturing cost. But a recent study has also highlighted its low carbon footprint and wastage as compared to other standard liquid delivery formats. Much of these benefits are realized because BFS only relies on virgin pharmaceutical-grade resin, and not energy intensive materials such as glass, metal, and rubber. Learn more here.
Dive into the manufacturing world of Blow-Fill-Seal
BFS is a growing around the world as a trusted fill-finish process for sterile liquids because of its advantages in efficiency, cost, and reliability. To learn more about BFS, visit our Expert Content Library and spend some time watching our wide range of introductory BFS videos on our Youtube channel.
Blow-Fill-Seal Expert Resources
Partnering for Success
Blow-Fill-Seal
Blow-Fill-Seal has a Compact Supply Chain
Related Video Content
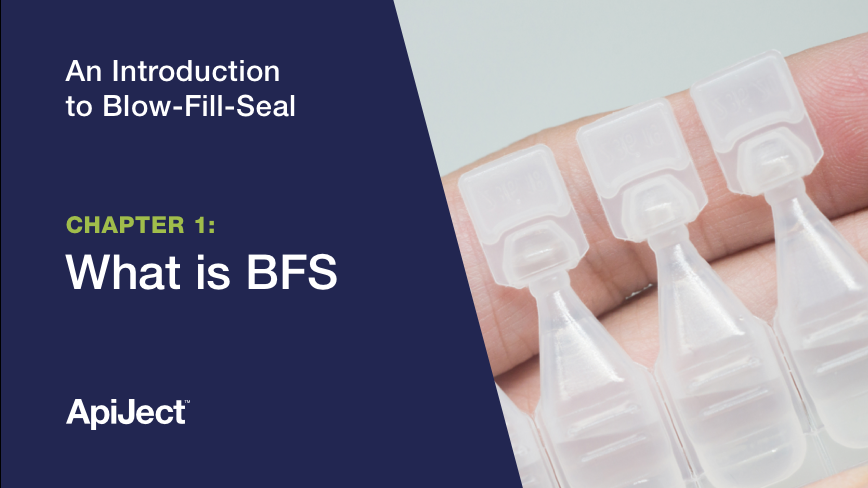
Intro to Blow-Fill-Seal / Chapter 1: What is BFS?
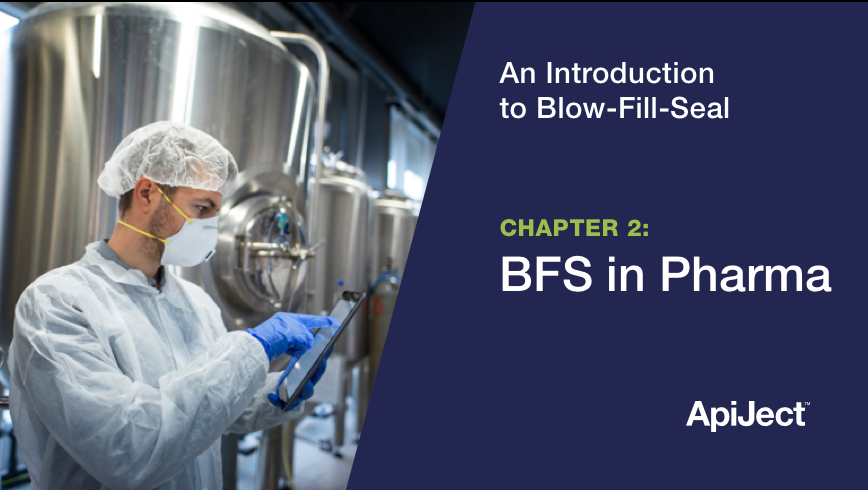
Intro to Blow-Fill-Seal / Chapter 2: Blow-Fill-Seal in Pharma
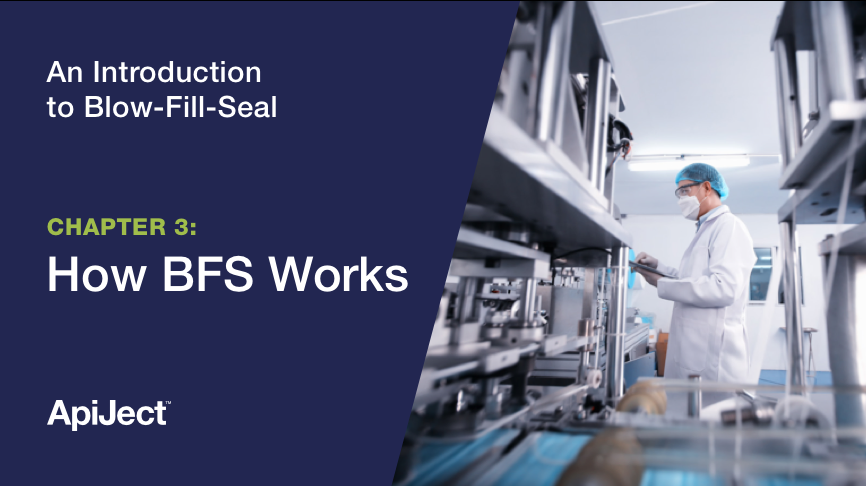
Intro to Blow-Fill-Seal / Chapter 3: How Blow-Fill-Seal Works
Get in Touch!
Contact us today to learn more about Apiject and easy first steps to see if our Platform may be right for your sterile liquid product.