Prototype
Testing
A wholistic and iterative process
All devices designed on the Apiject Platform go through a prototype creation and testing process that takes a device from concept to fit-for-purpose in its intended markets. This process includes the following phases:
- Prototype Creation: A 3D version of the prefilled injection device that all teams have agreed to pursue is 3D printed at our Studio One facility in London or a trusted advanced printing partner.
- Frontline Feedback: Depending on the intended market, our Device and Global Health teams will work with our frontline partners to put the prototype into the hands of healthcare workers and other intended users in the target markets.
- Prototype Refining: Based on that feedback we receive from these frontline focus groups, the potential device will go through a refinement process to better fit the device into its intended market. A new prototype device is then printed, and further focus group feedback may be undertaken.
From prototype concept to manufacturing
Once a prototype device has been refined to the point that all parties are happy with its market and supply chain fit, the development project enters a new stage where a commercial prototype is produced. This likely includes a Blow-Fill-Seal (BFS) container made from a BFS machine in the Apiject Technology Development Center and custom needle hubs produced by our manufacturing partners.
This commercial prototype is then taken through a series of performance tests and manufacturing assessments that put it on track for eventual regulatory submission and commercial development.
Explore device development with Apiject
To learn more about the Apiject device development process, visit our Expert Content section or contact our team of device and BFS experts today.
Prototype Expert Resources
Related Video Content
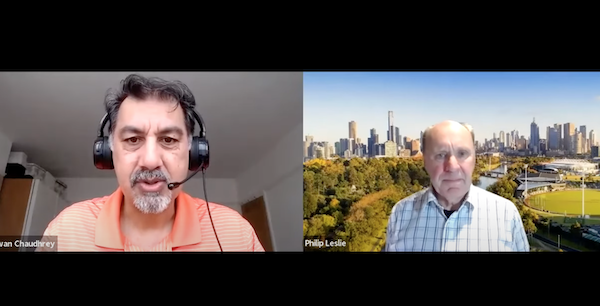
“How to Progress your Products in BFS”
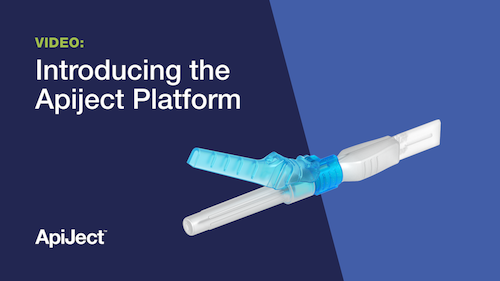
Changes are Coming to Prefilled Injectable Drug Delivery Systems
Get in Touch!
Contact us today to learn more about Apiject and easy first steps to see if our Platform may be right for your sterile liquid product.